Hey there, plastic enthusiasts! If you’re into manufacturing, you’ve probably heard of rotomolding—or rotational molding, if you want to get all technical about it. This versatile process is like the Swiss Army knife of plastic production, and it’s evolving faster than you can say “thermoplastic.” Let’s dive into the latest trends and innovations in the world of rotomolding and peek into the crystal ball to see where this industry is headed over the next five to ten years.
The Current Buzz in Rotomolding
Super-Strong Materials: Forget the old days of flimsy plastic parts. Today, rotomolding is all about durability. Manufacturers push the envelope with advanced materials like high-density polyethylene (HDPE) and cross-linked polyethylene (PEX). These materials are tougher and more resistant to impacts, and they can handle extreme temperatures. If you’re making something that needs to withstand the elements, rotomolding is your go-to.
Eco-Friendly Innovations: Sustainability is the name of the game. The industry embraces recycled materials like never before. Manufacturers are now using recycled plastics in the rotomolding process, reducing waste and cutting down on carbon footprints. Plus, there’s a push toward more energy-efficient manufacturing processes. Who knew being green could be so high-tech?
Multi-Layer Molding: Gone are the days of single-layer products. Today’s rotomolding can create parts with multiple layers, each with its own unique properties. This means better insulation, enhanced strength, and even custom colors all in one go. Think of it as the ultimate customization for your plastic parts.
Smart Molding Tech: Say hello! Welcome the future with smart rotomolding. New tech allows manufacturers to integrate sensors into the molding process. This means real-time data collection and analysis, leading to higher precision and fewer defects. It’s like having a plastic wizard overseeing every step of the process.
What’s Hot Now in Rotomolding?
Just in case you are curious, here are a few currently hot products made with rotomolding, showcasing the versatility and innovation in this manufacturing process. Each product link leads to its respective manufacturer for more details:
- Kayak – Kayaks made through rotomolding are popular for their durability and performance on water.
- Plastic Storage Containers – Rotomolding is perfect for creating heavy-duty, weather-resistant storage solutions.
- Trash Cans – Durable, long-lasting trash cans that withstand the elements and rough use.
- Playground Equipment – Rotomolded playground components are safe, colorful, and designed to last.
- Industrial Tanks – Large tanks used for storing chemicals, water, or other substances, built to be robust and leak-proof.
- Boat Hulls – Many small boats and canoes use rotomolding for their hulls due to its impact resistance and lightweight properties.
- Fuel Tanks – Rotomolded tanks are used in various industries for storing and transporting fuel.
- Dog Crates – Tough and durable dog crates made to withstand rough handling and provide safety for pets.
- Water Carts – Mobile water carts used in agriculture and landscaping for easy transportation of water.
- Medical Waste Containers – Specially designed containers for safely disposing of medical waste.
These products highlight how rotomolding can be applied across various industries to create durable, high-quality items. Check out the manufacturers for more detailed information about each product!
Peeking into the Future: What’s Next for Rotomolding?
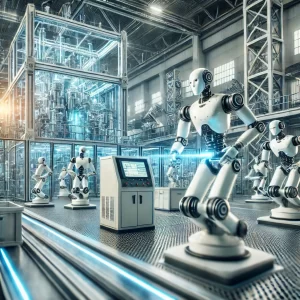
Advanced Materials: Now, we anticipate the next decade is set to bring even more exciting materials into the rotomolding mix. Expect to see more high-performance polymers that offer even greater strength and flexibility. Think space-age materials that could revolutionize how we design everything from automotive parts to consumer goods.
Two examples of high-performance polymers that could transform the rotomolding industry in the coming decade:
- Carbon Fiber Reinforced Polymers (CFRPs): Carbon fiber composites are already renowned for their exceptional strength-to-weight ratio and stiffness. As rotomolding technology advances, incorporating CFRPs could lead to the creation of even lighter and stronger automotive parts, aerospace components, and high-end consumer goods. Imagine rotomolded automotive panels or sports equipment that combine the durability of traditional materials with the advanced properties of carbon fiber.
- Ultrahigh Molecular Weight Polyethylene (UHMWPE): UHMWPE is known for its outstanding abrasion resistance and impact strength. This material is often used in demanding applications like ballistic protection and heavy-duty industrial equipment. In the next decade, UHMWPE could become more prevalent in rotomolding, leading to enhanced performance in products like rugged outdoor gear, high-strength containers, and durable industrial components.
Automation and Personalization
Automation and Robotics: Automation is on the rise, and rotomolding plays a part in this trend. Robotics will become increasingly sophisticated, handling everything from loading and unloading to quality control. This means faster production times and even higher precision. It’s like giving your factory a turbo boost.
ARBURG is at the forefront of integrating robotics with rotomolding. Their advanced automated systems handle tasks such as precise loading and unloading of molds, as well as sophisticated quality control through real-time monitoring and adjustments. This automation boosts production efficiency, reduces manual labor, and enhances the consistency and precision of rotomolded products. Imagine a factory where robotic arms seamlessly manage the entire rotomolding process, leading to faster turnaround times and superior product quality.
Increased Personalization: As consumer demand for personalized products grows, rotomolding will evolve to offer even more customization options. Imagine being able to order a custom-designed, one-of-a-kind plastic part straight from your smartphone. The future of rotomolding will make this a reality.
Enhanced Sustainability: The green wave will continue to roll through the rotomolding industry. Expect to see more innovations aimed at reducing environmental impact. This might include new recycling methods, biodegradable plastics, and even closed-loop systems where waste is reused in the production process.
For example, a rotomolding company could develop a new type of biodegradable plastic that breaks down naturally over time, reducing the amount of plastic waste in landfills. They might also implement a closed-loop system in their factory, where any leftover materials from the molding process are collected, reprocessed, and used to create new products, minimizing waste. Additionally, the company could introduce advanced recycling techniques that allow old or defective products to be broken down and remade into new items, further reducing their environmental footprint.
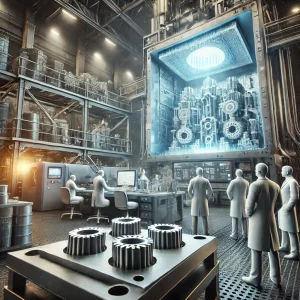
Integration with Other Technologies: Rotomolding will increasingly integrate with other cutting-edge technologies, like 3D printing and digital twins. This could lead to new ways of designing and producing parts, combining the best of both worlds for unprecedented efficiency and creativity.
A rotomolding company might start using 3D printing to create highly detailed molds or prototypes quickly. These 3D-printed molds could then be used in the rotomolding process to produce complex, custom-designed parts that would have been difficult or impossible to achieve with traditional methods. This integration allows for faster design iterations and more creative product development.
Another example could involve the use of digital twin technology, where a virtual replica of the rotomolding process is created to simulate and optimize production in real-time. Engineers could use the digital twin to test and refine designs before they are physically produced, ensuring greater accuracy and efficiency. This approach could reduce material waste, lower costs, and speed up the time-to-market for new products.
Rotomolding is in an exciting phase of transformation, blending advanced materials, eco-friendly practices, and cutting-edge technology. Whether you’re a manufacturer, designer, or just a curious onlooker, it’s clear that the future of rotomolding is bright and full of potential. Keep an eye on these trends, because the next five to ten years are bound to bring some jaw-dropping innovations. Stay tuned, and who knows—you might just be the next big thing in the world of rotomolding!